a nasty thought but for those of us living in the winter belt a necessary skill. I thought maybe you would be interested in seeing how I normally do this kind of thing. it will get long as it has a number of pictures and I can only post 10 at a time. nothing here is to cast doubt on someone else's work we don't know what or if they charged for it what the owners wanted at the time nor do we know how long this old repair lasted. before it failed. we only know it needed redone and I'm doing it differently they they did.. so the first this we do is. check things over notice the bad places and expose the damage
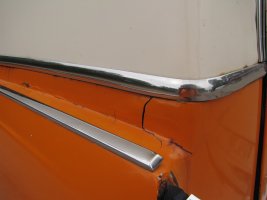
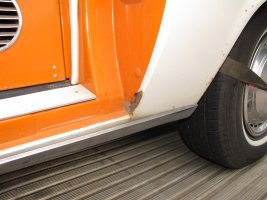
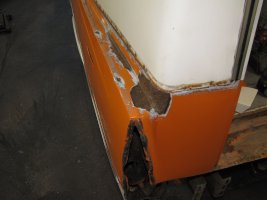
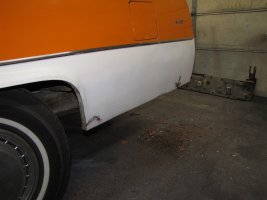
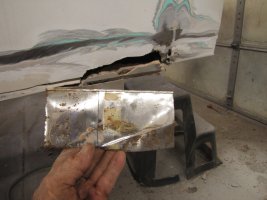
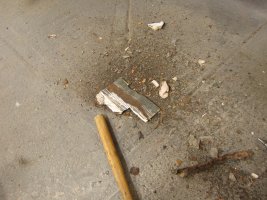
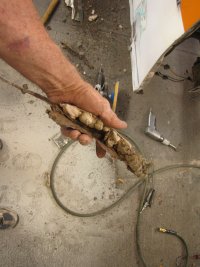
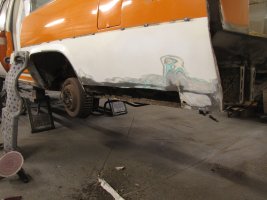
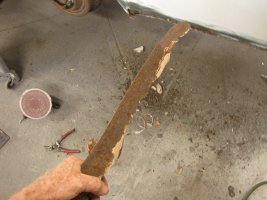
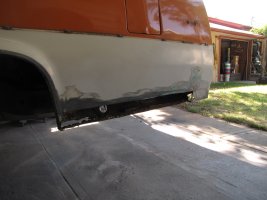
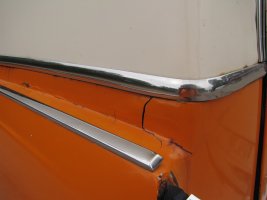
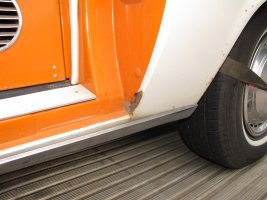
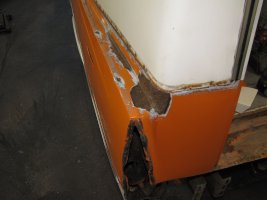
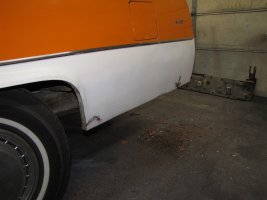
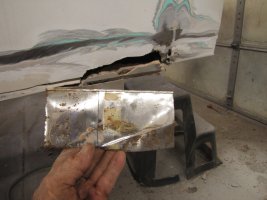
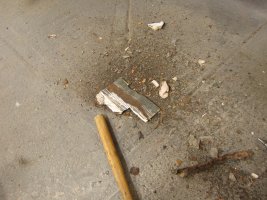
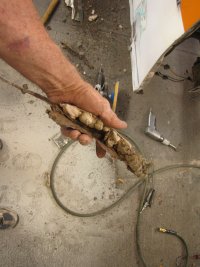
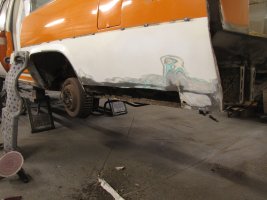
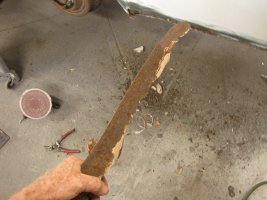
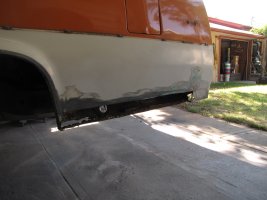
Last edited by a moderator: